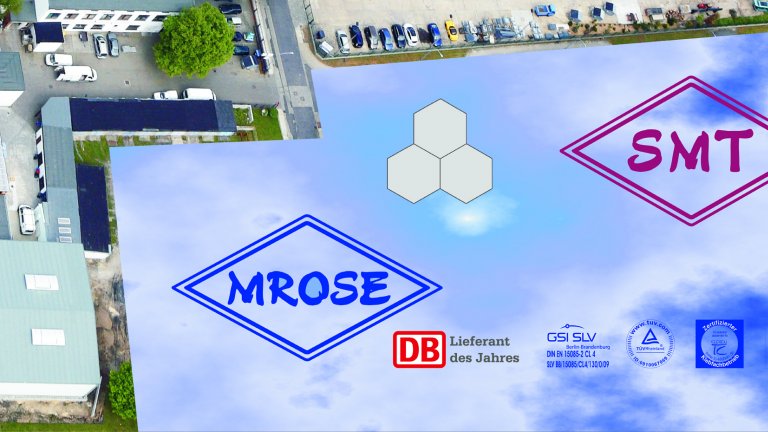
Forst Makes Sure that Trains are Cosily Warm
The requirements for the manufacturing of railway vehicles are steadily becoming more demanding. On the one hand, trains are supposed to be more and more comfortable and offer a high level of passenger safety, and on the other hand suppliers are being tasked with reducing the weight of individual components. Because weight costs money, throttles speed and consumes energy. The company System-Montage-Technik GmbH (SMT) from Forst fulfils these seemingly irreconcilable demands of the railway operators.
It is therefore no wonder that the company became a Q1 (Quality Level 1) supplier of the Deutsche Bahn AG. One of the decisive factors that made the small specialised business successful is its cooperation with regional research institutes, primarily the Brandenburg University of Technology Cottbus-Senftenberg.
The demand for all-in-one solutions based on a balanced combination of high-quality products led to the foundation of System-Montage-Technik GmbH in Forst in 2006. Almost 100 years before that, the cloth factory Mrose, which was re-privatised after the fall of the German Democratic Republic, had been founded in the very same place.
Under the management of the CEOs Max-Uwe Mrose and Christian Mrose, the family business became famous under the name “Technischer Handel Industriebedarf” (“Technical Trade Industrial Needs”) and rapidly expanded to become a country-wide full-range supplier of the industry dealing in all kinds of materials. Today, the 2,500 clients of Mrose can choose from about 80,000 products spanning a vast variety of diverse fields from occupational safety all the way to railings.
“The use of modern composite materials, such as glass- and carbon-reinforced plastics, is often very product-specific,” says Max-Uwe Mrose. “This is why we founded our subsidiary SMT that develops and manufactures components made of fibre composite systems specifically tailored to the wishes of its clients.”
In the past years SMT grew and became a successful producer of specifically tailored products. One example highlighting the capabilities of the company that already employs 18 people is the integration of an infrared heater into specifically developed sandwich panels.
Unprecedented heating system for mobile use
In addition to the main heating unit, two other systems, namely the single wire heating and the silicone mat heating, are currently being used in trains and railway vehicles. But traditional heating systems have disadvantages: they consume a lot of energy, they are prone to faults, they are distributing heat unevenly and their production is costly.
SMT now wants to develop a new type of functionally integrated system component; first for the flooring. It will consist of a medium completely coated with carbon nanoparticles which will be placed between panels and to which pressure and temperature will be applied. The result: an infrared heater with a significantly improved durability and maintainability and considerably reduced energy and production requirements.
This new product has made it through the demanding certification procedure of the Deutsche Bahn AG with great ease and SMT made it to the list of high-quality suppliers where it joined its parent company Mrose GmbH.
Reliance on external expertise
The decisive factor for the success of the product at the market was the cooperation with Panta Rhei, the research centre for lightweight construction materials in Cottbus at the Brandenburg University of Technology Cottbus-Senftenberg. Panta Rhei performed static and dynamic stress tests. Another partner was the then independent Higher Education Institution Lusatia. Their experts in the field of measurement and sensor technology constructed an infrared measuring station which was used to perpetually study and optimise heating patterns until the final product had the desired characteristics.
SMT GmbH also sought out the consulting services of Brandenburg Invest and of the Investment Bank (ILB) during this and during other research and development projects. “Without the support of the state in the form of low-interest loans and the fostering of networks, we would not have reached our current level of innovation,” Max-Uwe Mrose points out.