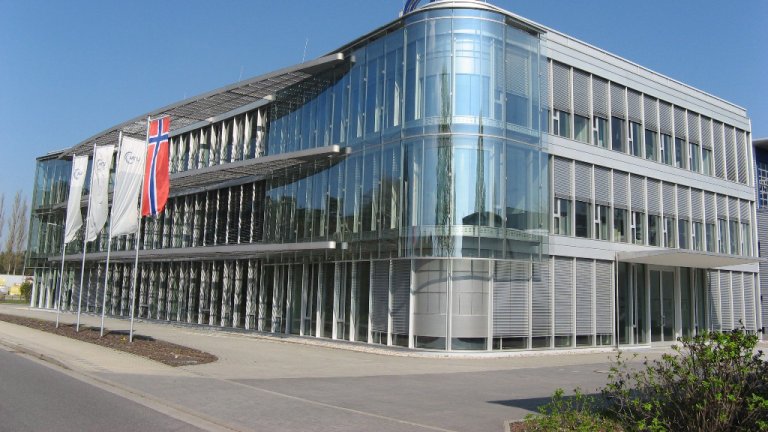
Creating Models of Engines in Test Beds
In order to study the performance characteristics of an aircraft engine in the test bed, it is necessary to observe, as closely as possible, how the engine operates. This holds especially true in the event of unforeseen problems during the test. This is why a minimalistic but informative instrumentation has been created for such testing.
Newly developed models can henceforth be used to make more accurate predictions about the performance of engines. It will now also be possible to study modifications to the test without needing to perform time-consuming and costly test runs.
Component-based performance analysis
The use of aero-thermodynamic models for determining engine and component properties is the established state of the art. Such models have also been used for the maintenance of CF34 engines at the location in Ludwigsfelde.
The performance of an engine in a test bed differs from the performance of an engine fitted to an airplane due to the interaction between the engine and the test bed as a whole. For example: in the case of an airplane, the air is being sucked in from the immediate surroundings, but in test beds the air has to pass through numerous deflecting and rectifying gratings, which reduces the performance and the efficiency of the engine. In order to make the performance in test beds more comparable to the actual normal performance of an engine fitted to an airplane, additional measures have to be implemented.
Designing integrated flow and performance models for the test bed
“Through our approach we want to be able to analyse and schematically describe the characteristics of the test bed in the same way we do it in the case of the engine,” explains project director Martin Marx. “Only by combining an engine model with a test bed model can we really evaluate the whole system during engine tests.” The changes within the fluid of the test bed are minor and the flow is very inhomogeneous, which makes it extremely difficult to choose the right measuring technology for the instrumentation and to create models.
In the end, to create models for the test bed, an interdisciplinary approach combining various specialist disciplines was used. On the one hand the test bed was – similarly to an engine – transferred into an aero-thermodynamic performance model that contributes e.g. to a better understanding of the impact the installations of the test bed have on engine performance. On the other hand an aerodynamic 3-D CFD model of the test bed was created, which, for example, helps to determine the impact of modifications to the test bed on the airstreams and therefore on the engine prior to their installation, which, in turn, makes costly test runs unnecessary. The two models have been designed and optimised by using their respective measurement data in an iterative mutual process.
The development of additional instrumentation
In order to be able to make precise observations, the right instrumentation was chosen by studying the engine as well as the test bed by conducting a series of in-depth studies. The project partner Fraunhofer Institute for Production Systems and Design Technology contributed considerably to the project; it provided additional test bed instrumentation which made it possible to calibrate and conclusively validate the CFD and the performance models.
“Thanks to the models we were able to develop a detailed understanding of the complex flow ratios in our test beds for the very first time,” explains Martin Marx, who is very satisfied with the project. He added: “The results form a solid basis for further improvements to our analysis skills.”
The project in this report was supported by funds from the Ministry for Economic Affairs and European Affairs of the State of Brandenburg and from the EU. The author is responsible for the content of this release.